People, who say, V/F mode is same good as vector mode, check please motor current in V/F mode and vector mode. I did it many times. May be i made some mistake, but in vector mode less motor current than V/F mode. At same speed and load of course. I did it with Telemecanique VFDs in the past, and now Gozuk VFDs. Many times less motor noise too. Of course, if you don't want to set or not possible to set correct motor parameters and autotuning, the result in vector mode could be very bad. As i know, vector mode is more accurate regulation, and it has best result. I know V/F mode as the first regulation method at the first variable frequency drive for 20 years. After that appeared the voltage flux vector regulation on the stator, and after that current flux vector regulation on the rotor. The last is the most accurate. My knowledge is not up to date. Write me please what are wrong in my statements, and what is the correct evolution of regulation.
Using variable frequency drives for the servo motor is quite possible, only if the application is not critical in positioning control purpose.
First you need to choose the variable frequency drive which is suitable for the particular motor and then you need to consider if the variable frequency drive have more number of inputs which can be used for various input functions. Nowadays most of the applications use AC induction motors so you need to choose the variable frequency drive with more functional options.
First you need to choose the variable frequency drive which is suitable for the particular motor and then you need to consider if the variable frequency drive have more number of inputs which can be used for various input functions. Nowadays most of the applications use AC induction motors so you need to choose the variable frequency drive with more functional options.
In order to understand this mystery, I believe you will find this short recap of power factor useful. A power factor is the ratio of "real power" and the "apparent power", also listed as cosine (Theta) of the angle between real power and apparent power of power triangle, where the hypotenuse is the apparent power, the horizontal is the real power and the vertical is the reactive power. This theta angle is also the same angle between the voltage and current waveforms at any given time.
In DC system it is easy to understand that the power transfer. It is simply voltage times the current drawn by the load. However in AC systems, it is not that simple because unlike the DC system, phase angle difference between the voltage and current waveforms makes big difference in the power consumed and transferred. Let's analyze these three scenarios and compute instantaneous power by simply multiplying voltage and current waveforms.
In DC system it is easy to understand that the power transfer. It is simply voltage times the current drawn by the load. However in AC systems, it is not that simple because unlike the DC system, phase angle difference between the voltage and current waveforms makes big difference in the power consumed and transferred. Let's analyze these three scenarios and compute instantaneous power by simply multiplying voltage and current waveforms.
It seems to me you need to design a state of the art test facility that enables you to test various motors for various voltages and powers. One gigantic VFD alone would not be enough anyway and running motors with a fraction of its output is just a wistful overkill plus harmonics etc. Unless you are testing at full load you won't need a full rated variable frequency drive, but starting a fixed speed motor in VFD mode is a problem as the exciter won't work at low speed.
VFD drive may have some problem with your motors. If you would like to check the efficiency you will not get the correct result due to the harmonics.
VFD drive may have some problem with your motors. If you would like to check the efficiency you will not get the correct result due to the harmonics.
All VFD manufacturers offer VFD programming training courses or "lunch and learns." These, when presented properly, can provide a great foundation to build upon.
Understanding the basics of how a variable frequency drive works is crucial to choose it. This should start with the fundamentals of magnetism, include details about how AC and DC motors operate, the role of speed and torque, and then how the variable frequency drive controls the stator and rotor of an AC motor by rectification and using transistors to invert DC voltage back to a voltage an AC motor can use to rotate.
Understanding the basics of how a variable frequency drive works is crucial to choose it. This should start with the fundamentals of magnetism, include details about how AC and DC motors operate, the role of speed and torque, and then how the variable frequency drive controls the stator and rotor of an AC motor by rectification and using transistors to invert DC voltage back to a voltage an AC motor can use to rotate.
The Active Front End acts as a controlled rectifier. Being a current-controlled inverter + filter, if the currents are controlled to be sinusoidal signals in phase (or in opposition) to the grid voltage, the result is power factor close to unity and low-order harmonics controlled to nearly zero.
On the other hand, DC bus capacitor voltage is controlled by regulating the amplitude and direction of currents coming from the grid. To increase its voltage, current is sunk from the grid (in-phase with voltage), while to decrease it current is sourced (regeneration).
On the other hand, DC bus capacitor voltage is controlled by regulating the amplitude and direction of currents coming from the grid. To increase its voltage, current is sunk from the grid (in-phase with voltage), while to decrease it current is sourced (regeneration).
1) Observe the bearing (and lubricant) temperatures. Are they starting to trend away from "normal" ... particularly upward? If so - there may be a problem.
2) Observe the acoustical sound of the bearing (using a very simple probe, like a wooden or steel dowel. or even a screwdriver). If it starts to sound different than normal, then things need to be examined more closely.
2) Observe the acoustical sound of the bearing (using a very simple probe, like a wooden or steel dowel. or even a screwdriver). If it starts to sound different than normal, then things need to be examined more closely.
Low Voltage VFD preventive maintenance is best performed on a periodic schedule, typically once per year. Consists mainly of visual inspection, cleaning with dry compressed air, checking connections for correct torque and setting up a replacement schedule for those components with the shortest operational life cycles. VFD cooling fans for example should be replaced every 3-5 years - Main bus capacitors every 7 years.
Don't retorque the connections. Use a thermal camera and check the variable frequency drive under load. If any connections show hot, THEN shut it down and check the torque with a torque wrench/screwdriver. I've seen more problems caused by people cranking down too hard on motor and power leads (and even control connections) than I have from connections that have worked loose.
Don't retorque the connections. Use a thermal camera and check the variable frequency drive under load. If any connections show hot, THEN shut it down and check the torque with a torque wrench/screwdriver. I've seen more problems caused by people cranking down too hard on motor and power leads (and even control connections) than I have from connections that have worked loose.
Harmonics in the electromagnetic torque, known as torque ripple or pulsating torque, exist in all electrical machines regardless of type or design. The harmonics are created by non-idealities in the electromagnetic fields produced by the rotor and stator interaction. Specifically, all permanent magnet (PM) based machines, irrespective of type, produce torque ripple that can be significant and create undesirable noise and vibration.
I'd look at the specifics of power or torque requirements that you have in your application and work with the local sales office to select an appropriate motor. Once you have a specific motor, it's been my experience, that you can determine the limitation of line starts per unit time. Again remember this is a thermal limit in large part, so oversizing or selecting a motor with a larger frame may be required. If this is not a viable solution, and your application can tolerate a subtle ramp, a VFD might be a way of minimizing the motor size (frame).
"...How load Torque requirements of a three phase induction motor can be fulfilled?...", it all depends upon the speed-torque characteristics of the load which can vary widely. The way to determine if the motor can accelerate the load and continuously run it at the proper speed is to plot the load's speed-torque curve on the motor's speed-torque curve.
As long as the motor provides more torque than the load requires at a given speed, the motor will be able to accelerate the load. If at any point the load curve plots above the motor torque, the motor will stall, so always provide an adequate margin for the motor torque including any voltage drop below its ratings.
As long as the motor provides more torque than the load requires at a given speed, the motor will be able to accelerate the load. If at any point the load curve plots above the motor torque, the motor will stall, so always provide an adequate margin for the motor torque including any voltage drop below its ratings.
If it's a 460V motor, the 1000V range should give a good indication. If the motor is 600 volts or less, 1000 to 2000 volt meggar is sufficient. Higher voltage meggar is fine, but no less than a 1000 volt and be sure the motor is disconnected from the VFD.
Featured Articles
Non-Enclosure Variable Frequency Drive ...
No enclosure (cover), reducing installation space and cost effective. Widely used in All-In-One control cabinet. Keep the same ...
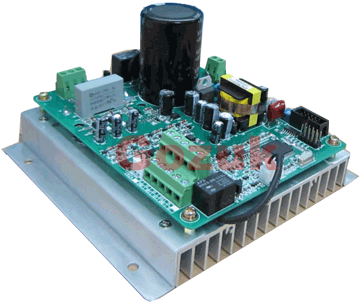
Variable frequency drive application ...
Variable Frequency Drive (VFD) can be used in lots of fields. Variable frequency drives are widely used to control the speed of ...
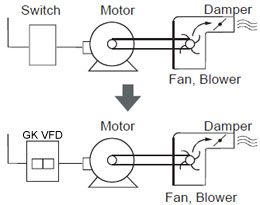
Variable frequency drive in HVAC ...
Variable frequency drives (VFD) have been used for HVAC systems in buildings for more than 40 years. But only in recent years, ...
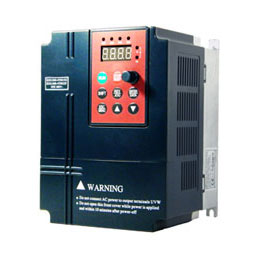
Variable Frequency Drive Harmonics and ...
A discussion of the benefits of variable frequency drives often leads to a question regarding electrical harmonic distortion ...
Three phase inverters
In the variable frequency drive rectifier paper, it explains how to go from three phase alternating current voltage to a direct ...
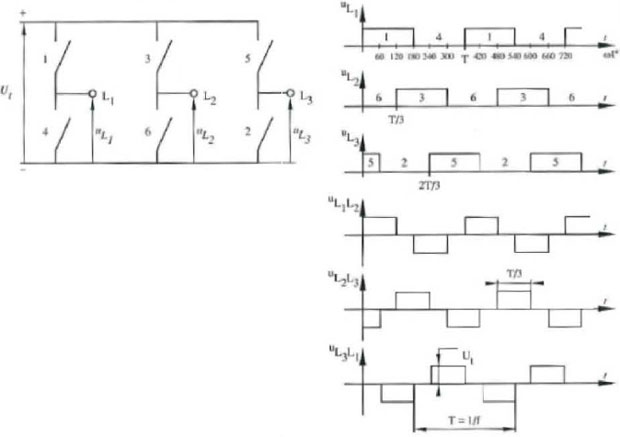
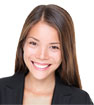
VFD manufacturers

