It is a fact that starting is by far the most stress on a motor; so minimize number of starts; but a motor in your ink-jet printer could start once every couple of seconds, a motor must perform the job it is designed for. This is where the concept of short time rating, variable frequency drive, soft start all becomes important and handy tools.
Let us also think of short time duty motors used in Rockets (missiles. launchers) where the motors in a stage , is allowed to burn out after, say a few seconds, once its job is over. Therefore, as suggested above, size, rating and application. What API states are applicable to only those ratings that are within the scope of laid down specifications. There are no laid down tests for the extreme duties, where the experience counts.
Let us also think of short time duty motors used in Rockets (missiles. launchers) where the motors in a stage , is allowed to burn out after, say a few seconds, once its job is over. Therefore, as suggested above, size, rating and application. What API states are applicable to only those ratings that are within the scope of laid down specifications. There are no laid down tests for the extreme duties, where the experience counts.
Safe Torque Off (STO) is a method the variable frequency drive (VFD) is disabled with no current or voltage going to the motor. Generally used in E-Stop schemes. The motor will coast to stop. Also the STO circuit has been qualified by a certified agency (the variable frequency drive has to meet certain requirements). The STO disables the output IGBT devices and is an integral part of the VFD hardware design.
If my motor rating is 150 KW...and my run of cable from variable frequency drive to Motor is 200 meter, then what size & type of cable to be used? How to calculate bearing current? Common-mode current?
I have never seen anyone attempt to calculate common mode currents. The amount of variables in motor types, cable capacitance, etc. does not make it practical. In a perfect world, I would have isolated bearings (on larger motors (75KW and larger, both ends) or shaft grounding. From practical experience, basic proper grounding is very important. From the power source to the variable frequency drive (VFD) and from the VFD to the motor. For your 200m application, I would also use either a du/dt filter or a sinus filter. You should not have any VFD operational issues at 200m with a 150KW system (from the VFD perspective), but if the project budget allows, I would use the insulated bearings OR an output filter. I am sure there are local manufactures for your project. I would discuss with the VFD manufacturer to ensure compatibility.
I have never seen anyone attempt to calculate common mode currents. The amount of variables in motor types, cable capacitance, etc. does not make it practical. In a perfect world, I would have isolated bearings (on larger motors (75KW and larger, both ends) or shaft grounding. From practical experience, basic proper grounding is very important. From the power source to the variable frequency drive (VFD) and from the VFD to the motor. For your 200m application, I would also use either a du/dt filter or a sinus filter. You should not have any VFD operational issues at 200m with a 150KW system (from the VFD perspective), but if the project budget allows, I would use the insulated bearings OR an output filter. I am sure there are local manufactures for your project. I would discuss with the VFD manufacturer to ensure compatibility.
What will happen to motor if we connect normal 3 Core wire armoured XLPE cable without individual screen for each phase to 3 pole of Motor? Why all core should be shielded for variable frequency drive (VFD) cable?
I've been applying variable frequency drives to industrial applications since 1986, and that was LONG before specialized VFD-rated cables came along. I have yet to personally see an application where the cable failed before the motor, though I have read about such failures in trade magazines. However, if I recall correctly these failures were all in unusual applications, not standard pump, fan, conveyor or machine applications. My one concession to the late 1980's switch to IGBTs is to recommend 1000V rated cable rather than 600V.
I've been applying variable frequency drives to industrial applications since 1986, and that was LONG before specialized VFD-rated cables came along. I have yet to personally see an application where the cable failed before the motor, though I have read about such failures in trade magazines. However, if I recall correctly these failures were all in unusual applications, not standard pump, fan, conveyor or machine applications. My one concession to the late 1980's switch to IGBTs is to recommend 1000V rated cable rather than 600V.
Using an IPM or SPM, you should be aware;
1. Use soft start, PM motor reach full speed/full torque nearly instantly. The shock load often damages connected mechanical components.
2. Voltage must be controlled.
3. You should not run more than 1 motor on 1 variable frequency drive (VFD).
4. VFD capacity must match motor (do not mix a 1hp VFD with a 1/2 hp motor).
Note; a spike can demagnetize the magnets leaving you with an expensive boat anchor.
1. Use soft start, PM motor reach full speed/full torque nearly instantly. The shock load often damages connected mechanical components.
2. Voltage must be controlled.
3. You should not run more than 1 motor on 1 variable frequency drive (VFD).
4. VFD capacity must match motor (do not mix a 1hp VFD with a 1/2 hp motor).
Note; a spike can demagnetize the magnets leaving you with an expensive boat anchor.
The best thing to do is obtain a sample of the product you want to pump and give that to the pump supplier of your choice, or have a chromatograph analyses ran on the product with the results to pass to the pump suppliers. The suppliers will run the results with your expected suction and planned head pressures to give you an accurate curve. I believe you are requesting this for a centrifugal pump and not a positive displacement pump. Some of the manufacturers also provide software to help with the pump sizing and provide curves at different rotational speeds if you get a pump with a variable frequency drive. The curves vary with pumps, product and conditions.
In general, using more than one tank is more expensive due to the extra fittings and connections required. As variable frequency drive (VFD) is very common, pressure tanks installed on discharge line are very small tank volume comparing a buster set without VFD.
Variable frequency drive with an adequate control system will try to keep pressure at a stated setpoint value. This means speed will match the pressure you define, at all variable Q demand. Much more stable than what you can expect from the classic ON / OFF pump - vessel design. VFD can be used with other control variables too, such as temperature for other pumping purposes (heating / cooling systems for e.g.).
Variable frequency drive with an adequate control system will try to keep pressure at a stated setpoint value. This means speed will match the pressure you define, at all variable Q demand. Much more stable than what you can expect from the classic ON / OFF pump - vessel design. VFD can be used with other control variables too, such as temperature for other pumping purposes (heating / cooling systems for e.g.).
As pumps are operated by electric motors and with the assistance of control systems, such as variable frequency drive (VFD). Decisions about pumps and mechanical seals involve both electrical and mechanical engineering considerations, however, the electrical decisions are based on mechanical situations. For instance, smaller pumps require higher starting horsepower for overcoming the starting torque requirement of the mechanical seal.
The Electrical Engineer has a valuable scope in pump industry concerning the drive unit and the different ways to start it --- according to the pump system --- and how to protect this power unit by selecting the suitable control panel with the right protection ways in it.
The Electrical Engineer has a valuable scope in pump industry concerning the drive unit and the different ways to start it --- according to the pump system --- and how to protect this power unit by selecting the suitable control panel with the right protection ways in it.
The third is to apply an electrical "brake" via a regenerative variable frequency drive (VFD) and/or dynamic braking resistor. Essentially, the dynamic braking resistor is a dumping ground for the energy contained in the rotating system, allowing it to be "bled off" as electrical energy. Because the operational mode has changed from motoring (power flow from VFD source to machine) to generating (from rotating machine to VFD), the VFD must be capable of supplying power in both directions - i.e. regenerate.
So here we were standing in the middle of the floor talking to the plant engineer watching our pump send vibrations through the floor strong enough to rattle your teeth. How am i able to explain that the pump should not run at 2200 rpm when it is designed for 1400 rpm and that the reason for the noise is the lack of NPSHa, or cavitation. All I am told is that the pump was not pumping enough at 1400 rpm so they had to increase the speed with the variable frequency drive (VFD). All I could say was they could run the pump at the proper speed and put a second pump in the system, or replace the bearings regularly and get a replacement pump on order. I expect the pump to last less than three months.
I am confident in saying this as I have over 20 years experience in this area. I've been responsible for making contractual performance guarantees on behalf of Gozuk Co Ltd (China) for nearly all of their largest projects for over 10 years. In some cases, the guarantees have included performance at reduced speed duty points at the VFD supply terminals. Furthermore, I've presented on this topic to water authorities, councils, consultants and large mining clients. Whilst there may not be a high static head in a water supply system, there is typically a minimum pressure setpoint which, if the pump is operated at relatively low speeds at those pressures, will induce a similar effect on pump performance.
On the variable frequency drive (VFD) for centrifugal pumps use there is a lot to teach and learn, however there are issues you should know - the best application for energy saving is using VFD in close circuit systems. The more static had you have proportional to dynamic head, you lose efficiency.
There is another hidden issue that many do not know, Motors above 30HP have to use special bearings (isolated ) so before you buying VFD for your motor check out if your motor suitable to be driven by VFD and also if needed additional cooling etc.
There is another hidden issue that many do not know, Motors above 30HP have to use special bearings (isolated ) so before you buying VFD for your motor check out if your motor suitable to be driven by VFD and also if needed additional cooling etc.
Featured Articles
Non-Enclosure Variable Frequency Drive ...
No enclosure (cover), reducing installation space and cost effective. Widely used in All-In-One control cabinet. Keep the same ...
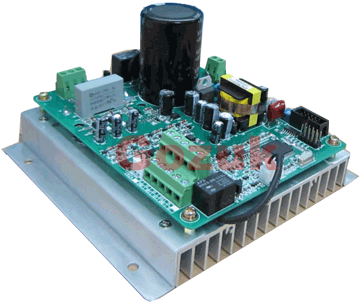
Variable frequency drive application ...
Variable Frequency Drive (VFD) can be used in lots of fields. Variable frequency drives are widely used to control the speed of ...
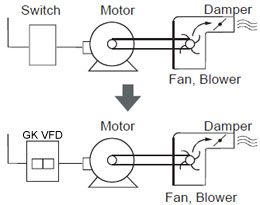
Variable frequency drive in HVAC ...
Variable frequency drives (VFD) have been used for HVAC systems in buildings for more than 40 years. But only in recent years, ...
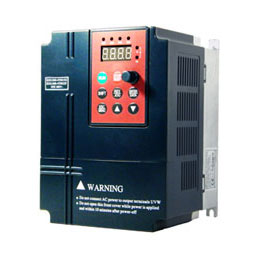
Variable Frequency Drive Harmonics and ...
A discussion of the benefits of variable frequency drives often leads to a question regarding electrical harmonic distortion ...
Three phase inverters
In the variable frequency drive rectifier paper, it explains how to go from three phase alternating current voltage to a direct ...
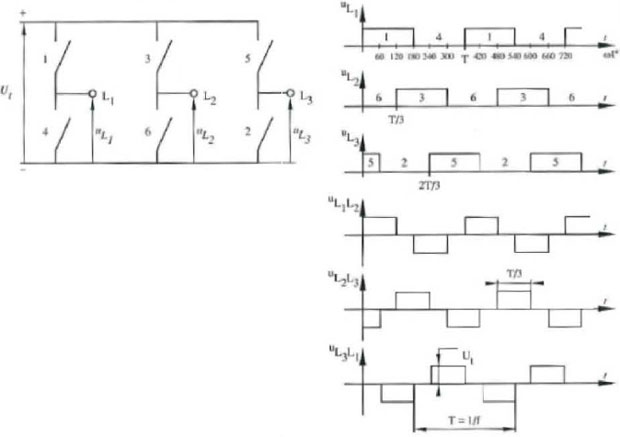
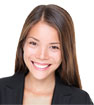
VFD manufacturers

