Specifying & Sizing VFD to enhance productivity
Following are some considerations to keep in mind to specify a VFD:
In contrast with machines in which all components are linked together like a big watch, individual control of multiple axes electronically provides ultimate edibility. How is this helpful? In applications such as packaging, where user needs change on an unpredictable schedule, retooling and changeovers waste the only thing users can't make more - time. Electronically controlled systems have significantly fewer mechanical components, so even in everyday operations such as cleaning and jam clearing, these compact, modern designs allow better access for shorter interruptions. Changeovers are done with touch screens, not tools, and recipes rather than wrenches.
When component faults, failures, and mishaps occur, across-line starter systems can't tell a designer what the conditions were just prior to the fault. Do they have Ethernet capability to allow remote access by personnel for quick problem solving? Can they monitor motor currents and other data for predictive maintenance? Probably not. In contrast, these functions are standard on many specified variable frequency drives. Unfortunately, many designers don't leverage all of these features.
Follow these tips to specify your VFDs:
Be sure to check application torque performance requirements (both steady state and dynamic) and select the appropriate VFD - either V/F, sensorless vector, full vector, servo, and so on. Don't forget to consider the application's environmental requirements. If a higher enclosure integrity is required (such as NEMA 12/IP55 or NEMA 4X/ IP66), some specified VFDs can provide this out of the box while others will have to be "enclosed" in a separate host enclosure to obtain these levels.
- Multitasking: Using a variable frequency drive may allow you to do several things at once instead of sequentially.
- Safety: Many variable frequency drives implement certified safety control; this means you may be able to allow motion to continue in areas where you previously required it to stop because of personnel safety. And even if stopping is required, say to clear a jam, certified integrated safety may prevent untimely and expensive procedures for preventing accidental motion.
In contrast with machines in which all components are linked together like a big watch, individual control of multiple axes electronically provides ultimate edibility. How is this helpful? In applications such as packaging, where user needs change on an unpredictable schedule, retooling and changeovers waste the only thing users can't make more - time. Electronically controlled systems have significantly fewer mechanical components, so even in everyday operations such as cleaning and jam clearing, these compact, modern designs allow better access for shorter interruptions. Changeovers are done with touch screens, not tools, and recipes rather than wrenches.
When component faults, failures, and mishaps occur, across-line starter systems can't tell a designer what the conditions were just prior to the fault. Do they have Ethernet capability to allow remote access by personnel for quick problem solving? Can they monitor motor currents and other data for predictive maintenance? Probably not. In contrast, these functions are standard on many specified variable frequency drives. Unfortunately, many designers don't leverage all of these features.
Follow these tips to specify your VFDs:
- Always verify the motor full load amperage (FLA) rating and choose a VFD size with an equal or higher amperage rating.
- Evaluate the environment in which the VFD will be located and choose an appropriate enclosure.
- Bigger size VFD is not always better - especially in torque control applications. VFDs that are drastically over-sized can have poor response in torque-control applications because here, the torque set point is only utilizing a small portion of overall torque resolution.
- Choose a right VFD that offers the right level of features for the application. VFDs that offer a staggering range of features also typically introduce a staggering level of complexity. Look for VFDs that are feature-rich, but also user friendly. A good benchmark for usability is the user manual. If the manual is several hundred pages long, then the VFD is likely to be complex and commissioning could be arduous.
- Where productivity is paramount (in other words, you want quick commissioning or to be able to quickly replace VFDs in the event of failure) choose a VFD with removable programmable memory. This allows VFD pre-programming for fast installation and commissioning. It also allows transport of configurations and parameter settings from an old VFD to a new VFD in the event of failure. This is especially productive for OEMs needing to duplicate VFD settings in every new machine they build. It can save many hours of programming time and eliminate human errors that are possible when programming by hand.
Be sure to check application torque performance requirements (both steady state and dynamic) and select the appropriate VFD - either V/F, sensorless vector, full vector, servo, and so on. Don't forget to consider the application's environmental requirements. If a higher enclosure integrity is required (such as NEMA 12/IP55 or NEMA 4X/ IP66), some specified VFDs can provide this out of the box while others will have to be "enclosed" in a separate host enclosure to obtain these levels.
very good
Post a Comment:
You may also like:
Featured Articles
Variable frequency drive Rectifier
To understand variable frequency drive (VFD) better, it's necessary to explain some of the main parts of the variable frequency ...
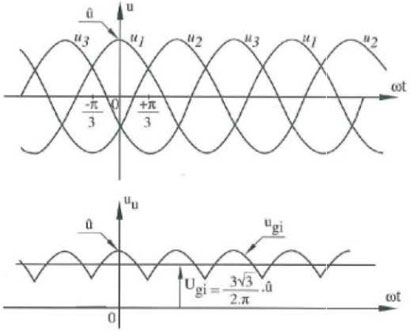
What is VFD, How it works? - VFD ...
VFD is shorted for Variable Frequency Drive (also known as AC Drives and Inverters) -- that's used to make an AC motor working in ...
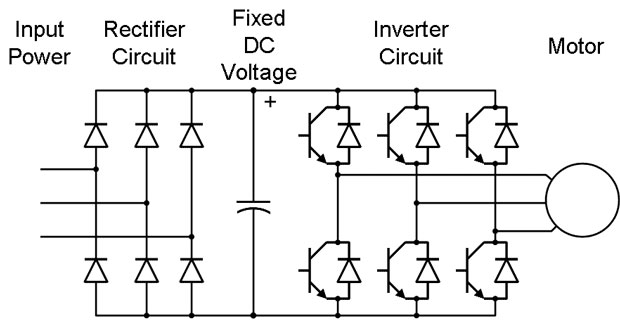
VFD: Insulated Gate Bipolar Transistor ...
IGBT (insulated gate bipolar transistor) provides a high switching speed necessary for PWM VFD operation. IGBTs are capable of ...
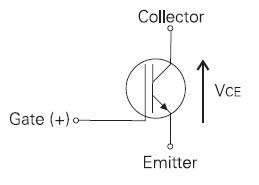
VFD controlled Induction motor ...
This paper presents a procedure to measure the efficiency on an induction motor fed by a VFD by the all operation range to speed ...
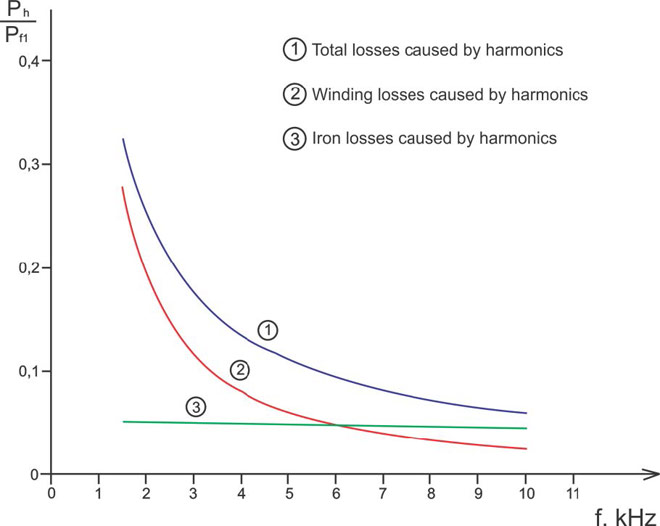
Three phase inverters
In the variable frequency drive rectifier paper, it explains how to go from three phase alternating current voltage to a direct ...
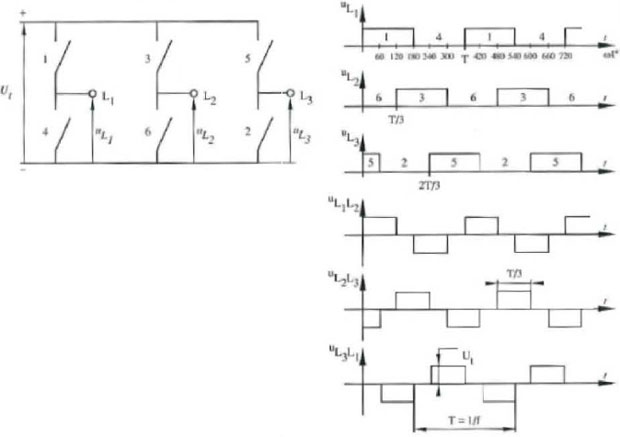
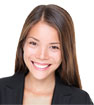
VFD manufacturers

