The variable frequency drives are designed according to the requirements and limit values of product norm EN 61800-3 with an interference immunity factor (EMI) for operation in industrial applications. Electromagnetic interference is to be avoided by expert installation and observation of the specific VFD information.
The variable frequency drives meet the requirements of the low-voltage directive 2006/95/EC and the requirements of the EMC directive 2004/108/EC. The EMC product standard EN 61800-3 relates to the VFD system. The documentation provides information on how the applicable standards can be complied if the variable frequency drive is a component of the VFD system. The declaration of conformity is to be issued by the manufacturer of the VFD.
The variable frequency drives meet the requirements of the low-voltage directive 2006/95/EC and the requirements of the EMC directive 2004/108/EC. The EMC product standard EN 61800-3 relates to the VFD system. The documentation provides information on how the applicable standards can be complied if the variable frequency drive is a component of the VFD system. The declaration of conformity is to be issued by the manufacturer of the VFD.
Just as we have acceleration and deceleration lanes on and off highways, VFDs have acceleration and deceleration ramps. These drives ramps are used to limit the motor starting current. They act as integrators in the loop dynamics. The variable frequency drive default setting usually is 5 sec. to 10 sec., a typical flow loop reset value. If the integrator in the PI or PID controller is set faster than the variable frequency drive ramp, the resulting closed-loop performance will exhibit a limit cycle. This cycle isn't due to reset windup or saturation but, rather, occurs because the controller integrator is acting faster than the load can respond. Many controllers offer a feature that allows the reset action to be changed based on actual valve travel. Configure an auxiliary variable frequency drive output signal proportional to the actual load to the controller function block to eliminate the limit cycle.
A computer program connected to the VFD or a human machine interface (HMI) front panel enables inputting data about the load and the motor as well as setting the VFD control strategy, which usually takes advantage of proprietary functionality. This variable frequency drives strategy together with the load dynamic behavior determines performance. Loops within the VFD electronics can be configured to control speed (through an external encoder), voltage, current and, in some cases, motor flux. These are the inner loops of the process control cascade. When tuning, remember that the inner loops must be at least five times more responsive than the outer loop. Another term to describe performance is bandwidth; it's inversely proportional to the time constant of the controller/motor with no load.
Variable frequency drive manufacturers offer models with varying performance and cost. So, assess which is the best VFD for the particular application.
Most VFDs have a defined, configured startup sequence that is to be run with the load disconnected. During this sequence the VFD powers the stator and makes measurements that determine the characteristics of the motor. These motor constants then are used to tune the internal electronic program.
Variable frequency drive manufacturers offer models with varying performance and cost. So, assess which is the best VFD for the particular application.
Most VFDs have a defined, configured startup sequence that is to be run with the load disconnected. During this sequence the VFD powers the stator and makes measurements that determine the characteristics of the motor. These motor constants then are used to tune the internal electronic program.
The variable frequency drive connecting cables must be protected externally, considering the maximum voltage and current values of the fuses. The mains fuses and VFD cable cross-sections are to be selected according to EN 60204-1 and DIN VDE 0298 Part 4 for the nominal operating point of the VFD. According to UL/CSA, the VFD is suitable for operation at a supply network of a maximum of 380 VAC which delivers a maximum symmetrical current of 5000 A (effective value) if protected by fuses of class RK5. Only use copper cables with a temperature range of 60/75 °C.
The VFD current source inverter (CSI) uses an SCR input to produce a variable voltage DC link. The inverter section also uses SCRs for switching the output to the motor. The current source inverter controls the current in the motor. The motor must be carefully matched to the VFD.
The manufacturer's specifications and instructions contained in the documentation must be complied with strictly during the variable frequency drive installation and commissioning. Before starting the relevant activity, read the VFD instructions of the manufacturers carefully and comply with the safety instructions.
Unauthorized opening and improper interventions of the variable frequency drives can lead to personal injury or material damage. Repairs on the VFDs may only be carried out by the VFD manufacturer or persons authorized by the manufacturer.
Unauthorized opening and improper interventions of the variable frequency drives can lead to personal injury or material damage. Repairs on the VFDs may only be carried out by the VFD manufacturer or persons authorized by the manufacturer.
IGBT's gave multiple benefits to VFD manufacturers: Being a field-effect transistor, the circuitry required to drive the base of the transistor was made much simpler, since large currents no longer needed to be injected on the base - just a voltage. This made the variable frequency drives more efficient - less parasitic power loss, much smaller power supplies. Also, because a fault current on the output of the VFD could be interrupted much better with a field-effect transistor, overall drive reliability improved greatly. Motor torque characteristics were improved because the output waveform simulated a sine wave better. And, of course, the motors were much quieter.
A lot of finger-pointing went on for a couple of years until the wire manufacturers came out with "inverter duty" cable, and motor manufacturers with "inverter duty" motors that could withstand the very fast switching. To my knowledge, you cannot buy a low-voltage (690V or below) VFD today that has anything but IGBTs in its inverter section.
A lot of finger-pointing went on for a couple of years until the wire manufacturers came out with "inverter duty" cable, and motor manufacturers with "inverter duty" motors that could withstand the very fast switching. To my knowledge, you cannot buy a low-voltage (690V or below) VFD today that has anything but IGBTs in its inverter section.
As modern variable frequency drives are based on micro-controllers with relatively large memories, there is an opportunity to fit the VFDs with software to provide sophisticated functionality that used to be restricted to DCS or dedicated controllers. The advantage of this software is that it is a tried and tested solution and therefore normally bug free. The other major advantage is that the software provides for standalone functionality and therefore the VFD does not require an interface to any PLC, DCS or automation system. However, this does not mean that any of these automation systems cannot be interfaced to the VFDs because there are plenty of fieldbus interfaces that allow control and monitoring of the VFDs. The most popular of these interfaces in South Africa are Profibus and Device Net. Any signal that is measured or calculated within the VFD is normally available for monitoring by the automation system - thus signals such as torque, power, speed, current, voltage and status are available and independent separate transducers to obtain these signals do not have to be installed.
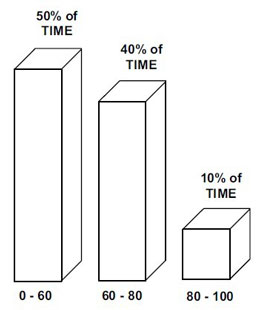
An existing variable air volume system uses dampers to regulate flow. The fan HP has been determined to be 20 HP and cost of electricity (including demand charges) is low 5c/KWH. The building is in operation 10 hours per day, 300 days per year, and the duty cycle is as described in following Figure.
1. The savings index = 1.00 (1500) + 0.80 (1200) + 0.55 (300) = 2,625
2. Savings/Year = 0.746 (20) (0.05) (2625) = $1,958.25
Costs were as follows:
Equipment less 10% $3,500.00
VFD installation 250.00
Engineering 000.00
Total Cost $3,750.00
Payback = $3,750 ÷ $1,958 = 1.9 years
This calculation allows potential variable frequency drive specifiers to make an informed decision before purchasing a variable frequency drive for their fan application. The calculator is intended as a first-pass indication tool to make a decision about whether a variable frequency drive will bring energy savings to a fan application.
In many applications there is a requirement that the torque loading (in the case of tight mechanical coupling) or speed (in the case of weak mechanical coupling) on two shafts driven by independent motors should be the same. This is easily satisfied through master/follower algorithms included within the variable frequency drive software and a communication regime between the VFDs.
One of the characteristics of a passive rectifier fed voltage source inverter type variable frequency drive is the near constant operational power factor of 0,95 from light to full load condition.
This feature does not depend on the pole number of the connected motor. VSIs with an active rectifier input can operate at unity or a leading power factor, if uitably sized, and therefore can be used to compensate for the lagging power factor loads that are also part of the plant network. Thus the need for additional power factor correction equipment or static VAR compensation equipment is eliminated or, at worst, reduced.
This feature does not depend on the pole number of the connected motor. VSIs with an active rectifier input can operate at unity or a leading power factor, if uitably sized, and therefore can be used to compensate for the lagging power factor loads that are also part of the plant network. Thus the need for additional power factor correction equipment or static VAR compensation equipment is eliminated or, at worst, reduced.
In certain processes a variable frequency drive is an essential part of the control system as without a means to start the process slowly, and slowly increase production rate, the process would be impossible to start or control. A typical example of this would be a paper machine where a slow start up is required and control of the speed of each stage of the machine depends on the previous stage and the required draw or stretch.
In the grinding mills used in minerals extraction from various ores, the addition of a variable frequency drive to control the mill speed provides an opportunity to compensate for variations in density, and other characteristics of the milled ore, by providing a further degree of freedom. This may lead to a decrease in specific energy consumption without sacrificing output product quality or daily production.
In the grinding mills used in minerals extraction from various ores, the addition of a variable frequency drive to control the mill speed provides an opportunity to compensate for variations in density, and other characteristics of the milled ore, by providing a further degree of freedom. This may lead to a decrease in specific energy consumption without sacrificing output product quality or daily production.
Featured Articles
Variable Frequency Drive Harmonics and ...
A discussion of the benefits of variable frequency drives often leads to a question regarding electrical harmonic distortion ...
Three phase inverters
In the variable frequency drive rectifier paper, it explains how to go from three phase alternating current voltage to a direct ...
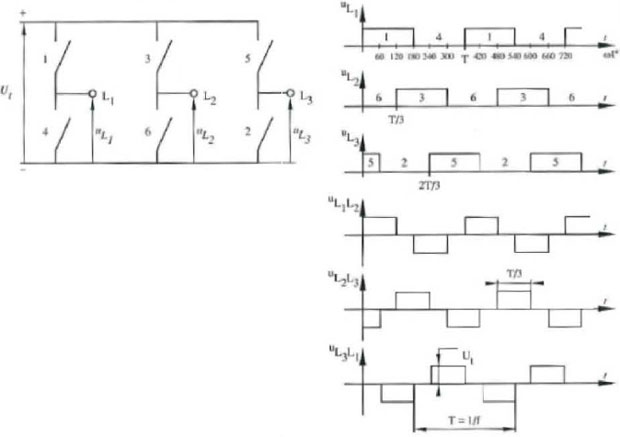
Variable frequency drive Advantages & ...
VFDs are good for variable speed, in a water pump this is used to maintain a steady pressure, they will smooth out variances in ...
Variable frequency drive Rectifier
To understand variable frequency drive (VFD) better, it's necessary to explain some of the main parts of the variable frequency ...
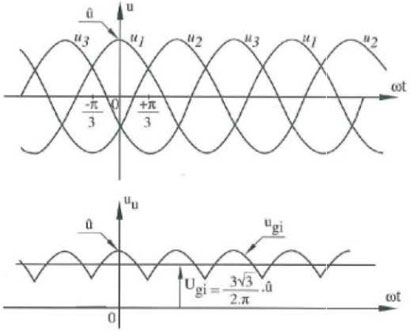
VFD controlled Induction motor ...
This paper presents a procedure to measure the efficiency on an induction motor fed by a VFD by the all operation range to speed ...
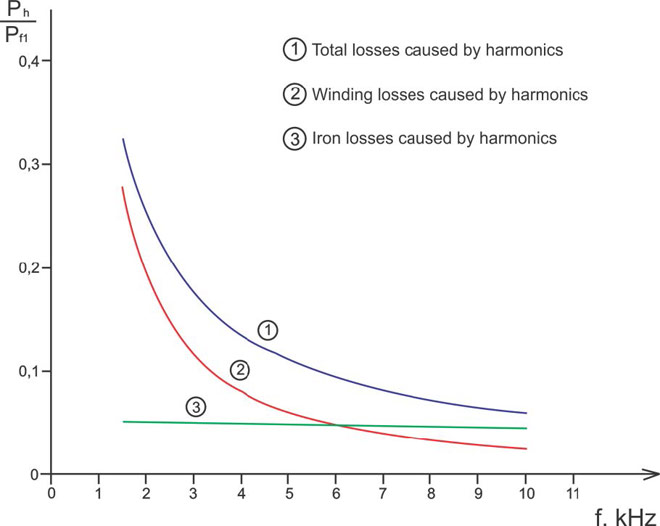
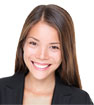
VFD manufacturers

