The "Cold Plate" variant enables installation of the variable frequency drive on suitable surfaces which have sufficient thermal conductivity to dissipate the heat developing during the operation of the variable frequency drive. Cooling is realized by means of a sufficient cooling area of the mounting plate or via an additional cooler.
The "Cold Plate" variant enables the use of the variable frequency drive in the following applications:
The "Cold Plate" variant enables the use of the variable frequency drive in the following applications:
- Installation in a housing, where a high type of protection is required but the volume of the housing limits thermal compensation.
- Use in highly polluted cooling air affecting the function and service life of the VFD fan.
- Use of several variable frequency drives in limited space conditions, e.g. installation of variable frequency drives on a liquid-cooled plate (sum cooler).
- Direct assembly on (or in) a machine case, with parts of the machine constructions taking over the cooling function.
The nominal values of the variable frequency drive apply to installation altitudes up to 1000 meters above sea level. If the VFD installation altitude exceeds 1000 meters, the drives output power and cooling agent temperature (ambient temperature) must be reduced.
The nominal values of the variable frequency drive apply to a cooling agent temperature between 0 and 40 °C (ambient temperature).
The nominal values of the variable frequency drive apply to a cooling agent temperature between 0 and 40 °C (ambient temperature).
During operation of VFDs, mechanical and electrical components are exposed to wear and tear. The service interval remaining until the next service (percentage of maintenance interval) of the following components can be monitored:
When the service interval until service has expired (value 0%), the variable frequency drive can indicate via the parameter. The behavior can be set up. The service interval remaining until service can be displayed via VFD parameters. Service is required as soon as the remaining service interval until maintenance has expired (value 0%). It must also be checked if the VFD component must be replaced.
- DC-link of variable frequency drive
- Fan of variable frequency drive
When the service interval until service has expired (value 0%), the variable frequency drive can indicate via the parameter. The behavior can be set up. The service interval remaining until service can be displayed via VFD parameters. Service is required as soon as the remaining service interval until maintenance has expired (value 0%). It must also be checked if the VFD component must be replaced.
Energy can be saved in a VFD by reducing the losses in the electric motor or by reducing the energy consumption of the variable frequency drive. In addition, the generator energy generated during braking operation can be used instead of converting it to heat.
The variable frequency drive offers the following energy saving options:
The variable frequency drive offers the following energy saving options:
- Standby mode of variable frequency drive
- Standby mode of operator panel
- Energy saving function: The operating point of the motor is optimized so that the power consumption is kept to a minimum.
- Quadratic V/f characteristic in the case of control of an asynchronous motor
- DC-link connection
- Energy-optimized braking
- PID controller (technology controller): When the reference value is reached, the motor is switched off.
- External DC 24 V power supply. Power supply can be switched off while the system is not in operation.
- Temperature-controlled fans
- Automatic switching frequency changeover
- In the variable frequency drive, special energy saving circuitry is integrated
With the variable frequency drive traverse function, a triangle-shaped frequency signal with the start-up and shutdown times to be set is superimposed on the VFD output frequency. The resulting chronological order of the reference frequency of master VFD and slave VFD are shown in the following diagrams. The function can be used, for example, for VFDs which wind up thread on coils in textile machines. To avoid winding errors at the turning point of the thread guide, a proportional step is performed which causes a quick speed change.
The rated values of the VFD are to be considered accordingly when it comes to dimensioning the application. The function of the motor circuit breaker can be linked to different data sets. In this way, it is possible
to operate different motors via one variable frequency drive. Thus, each motor can be equipped with its own motor circuit breaker.
In case a motor is operated via the VFD for which some setting values, e.g. minimum and maximum frequency, are changed via the data set switch-over, only one motor circuit breaker may be installed. This functionality can be set for single or multi-motor operation via variable frequency drive parameter.
to operate different motors via one variable frequency drive. Thus, each motor can be equipped with its own motor circuit breaker.
In case a motor is operated via the VFD for which some setting values, e.g. minimum and maximum frequency, are changed via the data set switch-over, only one motor circuit breaker may be installed. This functionality can be set for single or multi-motor operation via variable frequency drive parameter.
The variable frequency drive Field Oriented Control (FOC) systems are based on a cascade control and the calculation of a complex machine model. In the course of the guided commissioning, a map of the connected machine is produced by the parameter identification and transferred to various parameters. Some of these parameters are visible and can be optimized for various operating points.
The flux-forming current component is controlled by the field controller. The guided commissioning optimizes the variable frequency drive parameters of the field controller by measuring the time constant and magnetizing curve of the connected asynchronous motor. The parameters of the field controller are selected such that they can be used without changes in most applications. The proportional and the integrating part of the field controller are to be set via VFD parameters.
The flux-forming current component is controlled by the field controller. The guided commissioning optimizes the variable frequency drive parameters of the field controller by measuring the time constant and magnetizing curve of the connected asynchronous motor. The parameters of the field controller are selected such that they can be used without changes in most applications. The proportional and the integrating part of the field controller are to be set via VFD parameters.
The variable frequency drive configurations of the sensorless control contain the following additional functions, which supplement the behavior according to the parameterized V/f characteristic.
The load-dependent difference between the reference speed and the actual speed of the 3-phase motor is referred to as the slip. This dependency can be compensated by the current measurement in the output phases of the variable frequency drive.
The activation of Operation Mode for the slip compensation enables as speed control without feedback. The stator frequency and speed are corrected depending on the VFD load.
The load-dependent difference between the reference speed and the actual speed of the 3-phase motor is referred to as the slip. This dependency can be compensated by the current measurement in the output phases of the variable frequency drive.
The activation of Operation Mode for the slip compensation enables as speed control without feedback. The stator frequency and speed are corrected depending on the VFD load.
The variable frequency drive sensorless control in configuration is based on the proportional change of output voltage compared to the output frequency according to the VFD configured characteristic.
By setting the variable frequency drive V/f-characteristic, the voltage of the connected 3-phase motor is controlled according to the frequency. The torque to be applied by the motor at the corresponding operating point demands the control of the output voltage proportional to the frequency. At a constant output voltage/output frequency ratio of the variable frequency drive, the magnetization is constant in the nominal operating range of the 3-phase motor. The rating point of the motor or end point of the V/f-characteristic is set via the guided commissioning with the parameter Cut-Off Voltage and the parameter Cut-Off Frequency.
By setting the variable frequency drive V/f-characteristic, the voltage of the connected 3-phase motor is controlled according to the frequency. The torque to be applied by the motor at the corresponding operating point demands the control of the output voltage proportional to the frequency. At a constant output voltage/output frequency ratio of the variable frequency drive, the magnetization is constant in the nominal operating range of the 3-phase motor. The rating point of the motor or end point of the V/f-characteristic is set via the guided commissioning with the parameter Cut-Off Voltage and the parameter Cut-Off Frequency.
The VFD variable voltage inverter (VVI), also named Voltage Source Inverter (VSI), uses an SCR converter bridge to convert the incoming AC voltage into DC. The SCRs provide a means of controlling the value of the rectified DC voltage from 0 to approximately 600 VDC. The L1 choke and C1 capacitor(s) make up the DC link section and smooth the converted DC voltage. The inverter section consists of six switching devices. Various devices can be used such as thyristors, bipolar transistors, MOSFETS, and IGBTs. The following schematic shows an VFD that utilizes bipolar transistors. Control logic (not shown) uses a microprocessor to switch the transistors on and off providing a variable voltage and frequency to the motor.
Gozuk VFD specialists recommend connecting the motor to the variable frequency drive using shielded cables.
Variable frequency drive cables can be longer if sinus filters are used. By conversion in sinus-shaped currents, high frequency portions which might limit the VFD cable length are filtered out. Consider the voltage drop across the cable length and the resulting voltage drop at the sinus filter. The voltage drop results in an increase of the output current. The variable frequency drive must be suitable for the higher output current. This must be considered in the projecting phase.
- Connect the cable shield to PE potential properly, i.e. with good conductivity, on both sides.
- The motor cables must be kept physically separate from the control and network cables.
Variable frequency drive cables can be longer if sinus filters are used. By conversion in sinus-shaped currents, high frequency portions which might limit the VFD cable length are filtered out. Consider the voltage drop across the cable length and the resulting voltage drop at the sinus filter. The voltage drop results in an increase of the output current. The variable frequency drive must be suitable for the higher output current. This must be considered in the projecting phase.
The mains fuses and cable cross-sections are to be selected according to EN 60204-1 and DIN VDE 0298 Part 4 for the nominal operating point of the variable frequency drive. According to UL/CSA, approved Class 1 copper lines with a temperature range of 60/75°C and matching mains fuses are to be used for the VFD power cables. The electrical installation is to be done according to the variable frequency drives specifications and the applicable standards and directives.
The control, mains and motor lines must be kept physically separate from one another. The cables connected to the variable frequency drives may not be subjected to high-voltage insulation tests unless appropriate circuitry measures are taken before.
The control, mains and motor lines must be kept physically separate from one another. The cables connected to the variable frequency drives may not be subjected to high-voltage insulation tests unless appropriate circuitry measures are taken before.
Featured Articles
Variable Frequency Drive Harmonics and ...
A discussion of the benefits of variable frequency drives often leads to a question regarding electrical harmonic distortion ...
Three phase inverters
In the variable frequency drive rectifier paper, it explains how to go from three phase alternating current voltage to a direct ...
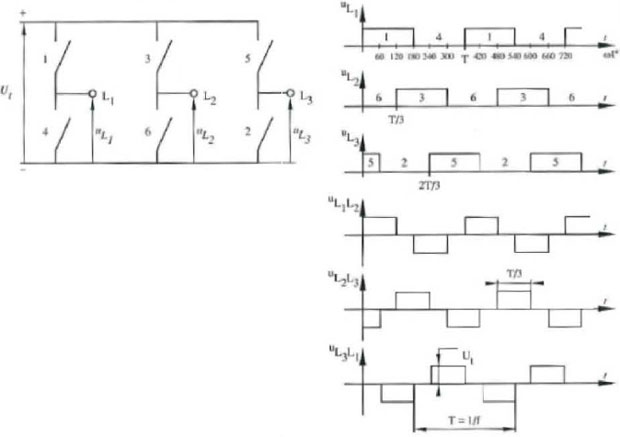
Variable frequency drive Advantages & ...
VFDs are good for variable speed, in a water pump this is used to maintain a steady pressure, they will smooth out variances in ...
Variable frequency drive Rectifier
To understand variable frequency drive (VFD) better, it's necessary to explain some of the main parts of the variable frequency ...
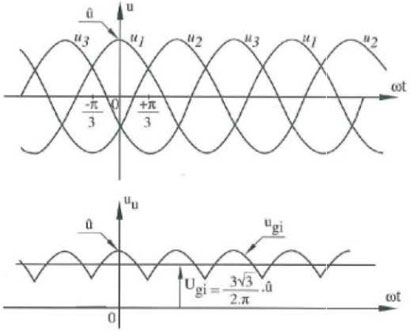
VFD controlled Induction motor ...
This paper presents a procedure to measure the efficiency on an induction motor fed by a VFD by the all operation range to speed ...
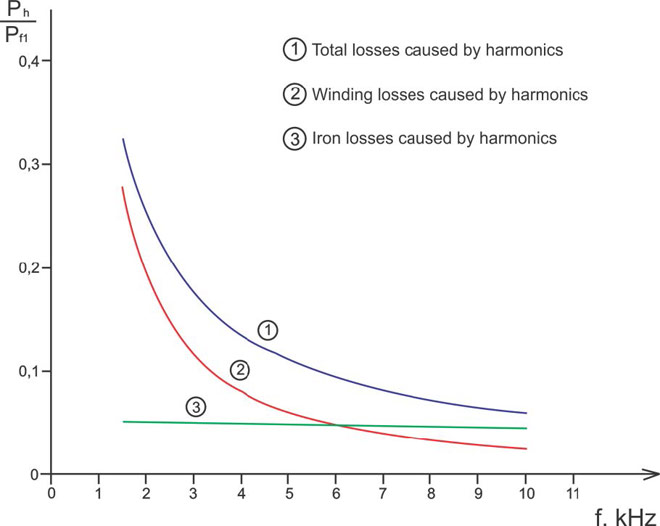
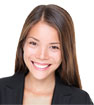
VFD manufacturers

