The variable frequency drive internal protection uses power semiconductor devices and complex electronic circuits to fulfill this function. Therefore consideration must be given to the effect of a failure of the function.
If a failure occurs, the final effect will be either:
If a failure occurs, the final effect will be either:
- (a) The vfd semiconductor device fails in an open circuit state in less than 0.4s
- (b) The vfd semiconductor device fails in the short circuit state for longer than 0.4s
A variable frequency drive runs a motor in such a way that you can increase or decrease the velocity of rotation by varying the frequency of the input signal i.e incoming AC voltage. In effect it converts a standard AC frequency that is typically 50 hz or 60 Hz to anything between 0 Hz and either 50 or 60 Hz.
A variable frequency drive is not a typical converter though it has conversions inside it. A converter would typically convert a DC signal to an AC signal vice versa. You do get variable frequency drives that can convert single phase AC to 3 Phase AC then in that case it is a converter but not a typical one.
A variable frequency drive is not a typical converter though it has conversions inside it. A converter would typically convert a DC signal to an AC signal vice versa. You do get variable frequency drives that can convert single phase AC to 3 Phase AC then in that case it is a converter but not a typical one.
The variable frequency drive is good at maintaining the rotor magnetism while reducing the frequency, since the VFD is designed for that. But most VFDs are not going to pass that energy back to the AC supply unless it has special circuitry to do so. If one busses many VFD drives together using the DC bus connection, the energy will flow back naturally and feed other loads. Otherwise the DC bus will overvoltage and often trip the variable frequency drive. A braking resistor is sometimes used to burn off the excess energy too.
With the new VFDs, there is a lot of radio frequency noise generated in the variable frequency drives and between the drive and the motors. Ultimately that noise wants to get back to the VFD from where it originated. This has led to shielding on the motor cables and the like. I had a problem at one plant with a 300KW motor and VFD, where many instruments were going crazy when the associated fan was started. After investigating I found that the cable between the motor and VFD was unsheilded but installed in conduit. I had the technician install a small wire between the conduit and the VFD chasis earthing pad, mind you not the panel earthing pad, and they thought I was crazy. All they could see was that both the panel and conduit where firmly connected through the plant ground grid, so this move made no sense. After they made the connection all the problems with instrumentation disappeared because we had short circuited the noise straight away back to the variable frequency drive.
1. You can even run more than 2 motors on a single variable frequency drive; it is absolutely OK, I am using it for quite a long time and the VFD is just working very fine.
2. In one application I had used 8 Motors (screw conveyors) on a single VFD (Gozuk make) we had no problem in that configuration.
3. In another application I used ABB 22KW VFD, to run 2x11 KW induction motors this was used on large EOT cranes and the motors were used for the long travel of the EOT cranes.
2. In one application I had used 8 Motors (screw conveyors) on a single VFD (Gozuk make) we had no problem in that configuration.
3. In another application I used ABB 22KW VFD, to run 2x11 KW induction motors this was used on large EOT cranes and the motors were used for the long travel of the EOT cranes.
VFDs are good for variable speed, in a water pump this is used to maintain a steady pressure, they will smooth out variances in line voltage and frequency. Some of the disadvantages are, most pumps won't push water if you slow the pump frequency down to less than 30Hz, unless you have a piston pump, as you slow the motor down you lose hp and the motor heats up more. For power efficiency, when you run near the designed frequency of the motor it is extremely efficient, but that efficiency drops off rapidly as you move away from that frequency.
You can use variable frequency drive to control a pump and maintain a fixed flow rate or pressure this in case that the demand is not constant, example : cold water to air conditioning units you do not need the same pressure or flow when only one unit is running so you slow down the pump speed but when you need 3 or more working you increase the speed.
You can use variable frequency drive to control a pump and maintain a fixed flow rate or pressure this in case that the demand is not constant, example : cold water to air conditioning units you do not need the same pressure or flow when only one unit is running so you slow down the pump speed but when you need 3 or more working you increase the speed.
To understand variable frequency drive (VFD) better, it's necessary to explain some of the main parts of the variable frequency drive. The main two parts of a VFD are the rectifier and the inverter. The first will convert the AC voltage into a DC voltage; the second will convert this DC voltage into an AC voltage with variable magnitude and frequency. So together they form an AC to AC converter tool which can be placed between the normal electric grid and a load with a special demand for voltage and frequency characteristics.
The paper presents the effect of instrument accuracies on the overall uncertainty in efficiency measurement described as in direct input-output methods as per IEC 60034-2-1. The measurement instrumentation normally has higher error margins for variable frequency drive supply conditions as compared to sinusoidal supply. This results in higher values of estimated uncertainty in efficiency during measurement under variable frequency drive supply conditions. The efficiency measurement is performed on an induction motor under both sinusoidal and VFD controlled supply conditions at rated speed. The percentage increase in motor losses during VFD controlled supply is found to be linearly increasing with respect to load condition. This is very different observation than the assumption made in IEC 60034- 2-3 that the additional motor loss due to VFD controlled supply is independent of motor loading.
Then the uncertainty estimation is performed on measured efficiency under both sinusoidal and VFD controlled supply conditions. It is observed from estimated uncertainty values are below maximum limits described as per IEC 60034-1 standard specification when measurements are performed with line filter functions in power analyzers is disabled. This is applicable for both sinusoidal and VFD control measurement tests. But measurement uncertainty is much higher when line filters are activated for measurements with variable frequency drive supply conditions. In this situation, the estimated uncertainty values are very close or higher than allowed tolerance limits. It is recommended that the use of line filters should be avoided under such situations.
Then the uncertainty estimation is performed on measured efficiency under both sinusoidal and VFD controlled supply conditions. It is observed from estimated uncertainty values are below maximum limits described as per IEC 60034-1 standard specification when measurements are performed with line filter functions in power analyzers is disabled. This is applicable for both sinusoidal and VFD control measurement tests. But measurement uncertainty is much higher when line filters are activated for measurements with variable frequency drive supply conditions. In this situation, the estimated uncertainty values are very close or higher than allowed tolerance limits. It is recommended that the use of line filters should be avoided under such situations.
This paper presents a procedure to measure the efficiency on an induction motor fed by a VFD by the all operation range to speed and torque. The paper describes the procedure, and accuracy requirements of the instrumentation required by international standards and research results to ensure the measurement of real efficiency of induction motors and VFDs. Also, describes the basic measurement requirements of the variables, accurate data measurement, information processing, power and efficiency calculations. The paper describes and analyzes the different power calculations implemented and researched, which correspond to algorithms used by the commercial instrumentation. The losses on the induction motor–VFD system are shown and analyzed. Finally, the procedure for efficiency measurement is implemented through lab tests.
IGBT (insulated gate bipolar transistor) provides a high switching speed necessary for PWM VFD operation. IGBTs are capable of switching on and off several thousand times a second. A VFD IGBT can turn on in less than 400 nanoseconds and off in approximately 500 nanoseconds. A VFD IGBT consists of a gate, collector and an emitter. When a positive voltage (typically +15 VDC) is applied to the gate the IGBT will turn on. This is similar to closing a switch. Current will flow between the collector and emitter. A VFD IGBT is turned off by removing the positive voltage from the gate. During the off state the IGBT gate voltage is normally held at a small negative voltage (-15 VDC) to prevent the device from turning on.
Pulse Width Modulation (PWM) VFDs provide a more sinusoidal current output to control frequency and voltage supplied to an AC motor. PWM VFDs are more efficient and typically provide higher levels of performance. A basic PWM VFD consists of a converter, DC link, control logic, and an inverter.
The VFD manufacturer did additional research to identify some probable causes. The contractor needed to provide a proper earth ground, ground the controller and the motor to this proper earth ground, and use insulated bushings to isolate other devices from the controller and motor to prevent grounding to or through the water piping system. These recommendations are, generally, requirements of the National Electrical Code, but they are sometimes overlooked. An additional suggestion would have been to try an isolation transformer. The VFD manufacturer subsequently confirmed the transformer may not have helped in absence of a proper earth ground.
Featured Articles
Variable Frequency Drive Harmonics and ...
A discussion of the benefits of variable frequency drives often leads to a question regarding electrical harmonic distortion ...
Three phase inverters
In the variable frequency drive rectifier paper, it explains how to go from three phase alternating current voltage to a direct ...
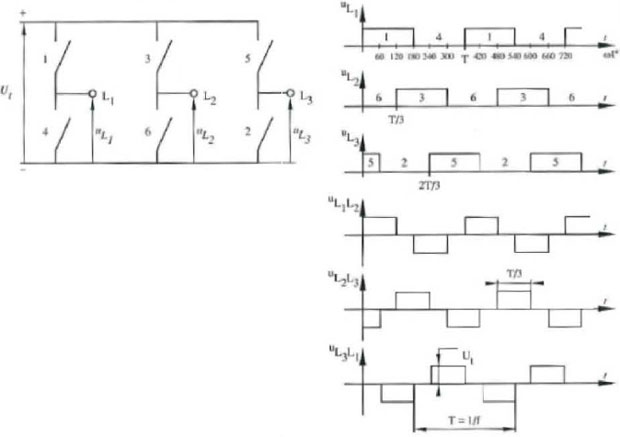
Variable frequency drive Advantages & ...
VFDs are good for variable speed, in a water pump this is used to maintain a steady pressure, they will smooth out variances in ...
Variable frequency drive Rectifier
To understand variable frequency drive (VFD) better, it's necessary to explain some of the main parts of the variable frequency ...
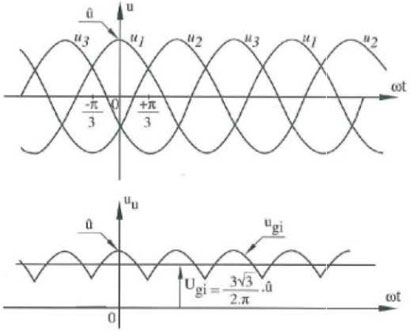
VFD controlled Induction motor ...
This paper presents a procedure to measure the efficiency on an induction motor fed by a VFD by the all operation range to speed ...
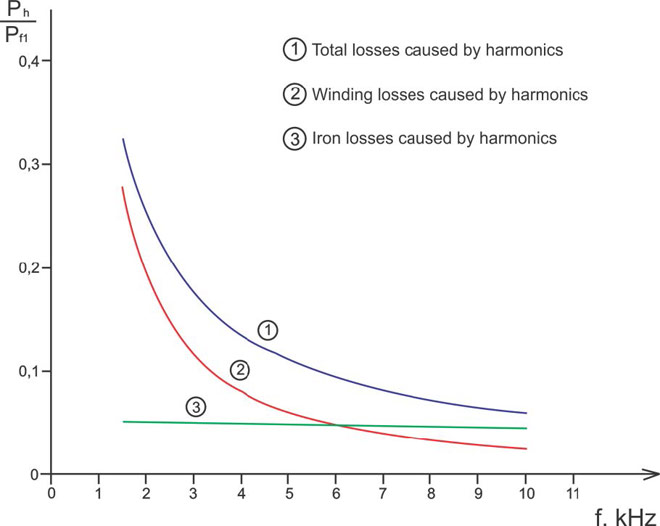
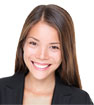
VFD manufacturers

