Some manufacturers provide additional circuits inside the VFD to allow the input of closed-loop feedback signals from encoders or resolvers. These circuits will decode the signals from the sensors and scale them to the level required. This feature makes the VFD operate more like a package system. This also makes it easier for design engineers to put a complete system together where all of the components match, Gozuk named this VFD with closed-loop capability a vector VFD. Its scalar VFD can be operated as either an open-loop or closed-loop VFD. Other manufactures provide similar packages. It is important to remember that the vector and scalar VFDs are more expensive and more complex than a simple VFD.
The VFD can be operated as a stand-alone unit or it can be controlled by a PLC or other electronic control system that sends a 0-10 volt or a 4-20 mA signal. When the VFD is operated as a stand-alone system, a potentiometer may be provided directly on the face of the VFD. The operator of the machinery can set the speed for the VFD by adjusting the potentiometer from 0-100%. In some applications, the potentiometer is mounted on the machine's front panel instead of on the face of the VFD. The reason for this is that in some cases the VFD must be mounted in an electrical cabinet, and the potentiometer on the face of the VFD is not accessible when the electrical cabinet's door is closed.
The main VFD program is contained in the processor's firmware & not normally accessible to the variable frequency drive user. A parameter is a variable associated with the operation of the VFD that can be programmed or adjusted. Parameters provide a degree of adjustment so that the user can customize the VFD to suit specific motor & driven equipment requirements. The number of parameters can range from 50, for small basic VFDs, to over 200 for larger, more complex VFDs. Some variable frequency drives provide upload/download & parameter copy capability. Common adjustable parameters include the following:
- Preset speeds
- Minimum & maximum speeds
- Acceleration & deceleration rates
- Two- & three-wire remote control modes
- Stop modes: ramp, coast, DC injection
- Automatic torque boost
- Current limit
- Configurable input jog
- V/Hz settings
- Carrier frequency
- Program password
Most variable frequency drive applications require the AC motor to run at a specific speed as set by the keypad, speed potentiometer, or analog input. Some VFDs provide an alternative option that allows precise process control through a setpoint controller or PID mode of operation. Many VFDs come equipped with a built-in proportional-integral-derivative (PID) controller.
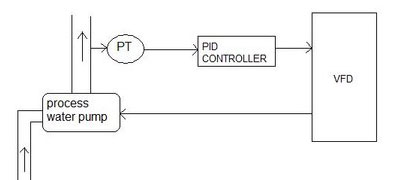
The PID loop is used to maintain a process variable, such as speed. The desired speed, or setpoint & the actual speed values are input to a summation point. These two signals are opposite in polarity & yield a zero error or deviation whenever the desired speed equals the actual speed.
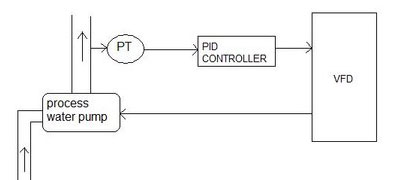
The PID loop is used to maintain a process variable, such as speed. The desired speed, or setpoint & the actual speed values are input to a summation point. These two signals are opposite in polarity & yield a zero error or deviation whenever the desired speed equals the actual speed.
The evolution of VFD technology has seen many changes in a relatively small time frame. As a result, newer VFDs with greater functionality are now avail able. Most VFDs manufactured today are pulse-width modulation VFDs that convert the 60-Hz line power to direct current, then pulse the output volt age for varying lengths of time to mimic an alternating current at the frequency desired. Many older variable frequency drives were distinguished by the type of inverter circuitry used in the VFD. Two earlier types of VFDs were the voltage-source inverter & the current-source inverter.
Derating a variable frequency drive means using a larger than normal VFD in the application. Derating is required when a VFD is to be operated outside the normal operating range specified by the manufacturer. Most VFD manufacturers provide derating figures when the VFD is to be operated outside the specified temperature, voltage, & altitude. As an example, derating must be considered when the VFD is installed at high altitude, greater than 1000 meters (3300 ft.). The cooling effect of the VFD is deteriorated because of the reduced density of the air at high altitudes.
Motor specifications are programmed into the variable frequency drive to ensure optimum drive performance as well as adequate fault & overload protection. This may include the following items found on the nameplate, or derived through measurements:
Frequency (hertz) - Nameplate frequency required by the motor to achieve base speed. The default value is normally 60 Hz.
Frequency (hertz) - Nameplate frequency required by the motor to achieve base speed. The default value is normally 60 Hz.
Following diagram shows typical input digital connections for two-wire or three-wire control with stop, forward, reverse, & jogging functions. Because variable frequency drives are electronic devices, they can have only one phase rotation output at a time. Therefore, interlocking, as required on electromechanical devices, is not required for variable frequency drive for ward/reverse operations. Inputs can also be programmed for two- or three-wire control to accommodate either maintained or momentary start methods. Note that the control logic is determined & executed by the program within the VFD & not by the hard-wiring arrangement of the input control devices.
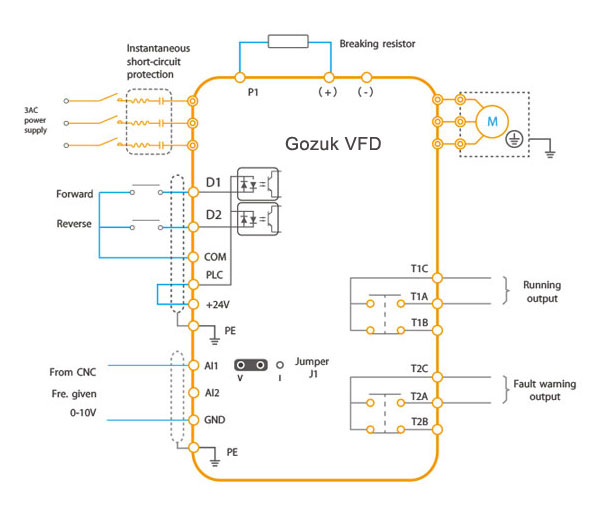
The figure illustrates typical power & control inputs & output termination points found on variable frequency drives. The three phase power source is connected at the line input terminals L1, L2, & L3 & the motor feed conductors are connected to the output motor terminals T1, T2, & T3.
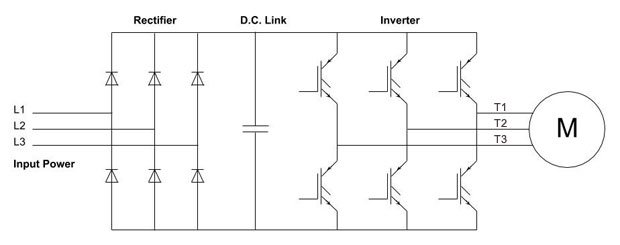
VFDs offer many of the same advantages as reduced-voltage & soft start starters. The timed speed ramp-up feature found in variable frequency drives is similar to the soft start function of starters. However, the variable frequency drive timed speed ramp-up generally has a much smoother acceleration than soft starting, which is usually done in steps. Soft starting with a variable frequency drive reduces the frequency initially supplied to the motor & steps up the frequency over a preset period of time. Variable frequency drives with soft start capabilities have replaced many of the older types of reduced-voltage starters. While variable frequency drives offer soft start capabilities, true soft start starters are not considered VFDs.
In most VFD applications the VFD itself provides overload protection for the motor. However, the feeder cable can't be protected by variable frequency drive built-in protection. The motor VFD provides protection based on motor name plate information that is programmed into it. VFDs incorporate many complex protective functions, such as:
- Stall prevention
- Current limitation & overcurrent protection
- Short-circuit protection
- Undervoltage & overvoltage protection
- Ground fault protection
- Power supply phase failure protection
- Motor thermal protection through sensing of the motor winding temperature
Safety in operation & maintenance dictates that all motor-operated equipment has a means of fully disconnecting the power supply. This is a requirement of National Electrical Code (NEC) & Occupational Safety & Health Administration (OSHA) regulations. As with starters, to reduce cost & size, most variable frequency drive manufacturers don't provide a disconnect switch as part of their standard variable frequency drive package. If the optional input disconnect is not specified, a separate switch or circuit breaker must be installed. Article 430.102 of the NEC includes requirements for disconnecting means for the motor itself & for the motor drives; both sets of requirements must be satisfied.
Featured Articles
Variable Frequency Drive Harmonics and ...
A discussion of the benefits of variable frequency drives often leads to a question regarding electrical harmonic distortion ...
Three phase inverters
In the variable frequency drive rectifier paper, it explains how to go from three phase alternating current voltage to a direct ...
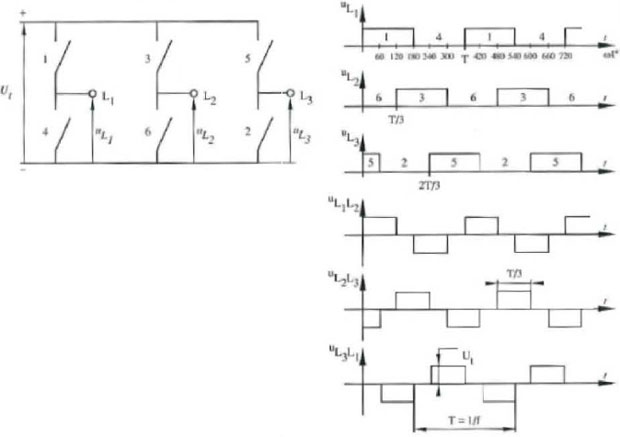
Variable frequency drive Advantages & ...
VFDs are good for variable speed, in a water pump this is used to maintain a steady pressure, they will smooth out variances in ...
Variable frequency drive Rectifier
To understand variable frequency drive (VFD) better, it's necessary to explain some of the main parts of the variable frequency ...
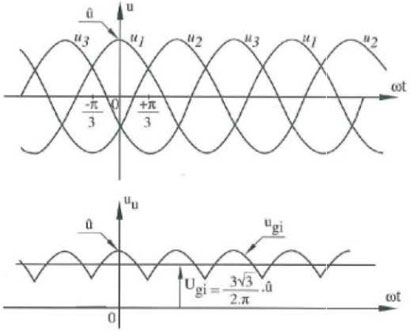
VFD controlled Induction motor ...
This paper presents a procedure to measure the efficiency on an induction motor fed by a VFD by the all operation range to speed ...
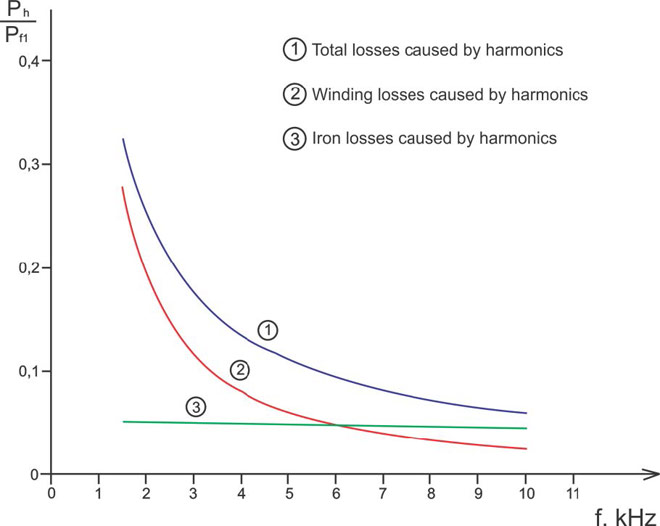
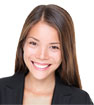
VFD manufacturers

